September 15, 2021
Central American Copper Mine: Supporting Dewatering Upgrades
Capturing rising water levels at one of the world's largest copper mines in a short time frame could have been a substantial hurdle for majority mine owner First Quantum Minerals.
However some innovation by Coerco delivered a quick solution that could be assembled in-situ to take advantage of the massive influx of water. First Quantum Minerals were seeking to push its existing, large dewatering system at its Cobre Copper mine operation in Panama into areas with deeper water deposits.
Lateral thinking leads to big solutions
The ability to quickly access dozens of large-scale pipe floats to support the new discharge pipes by 250 metres required a manufacturer that could think outside the box.
As the industry leader in dewatering solutions, Coerco was entrusted by First Quantum Minerals with the mammoth task of creating the large number of Multi Float® pipe floats to be incorporated seamlessly onto its dewatering system.
The ability to quickly access dozens of large-scale pipe floats to support the new discharge pipes required a manufacturer that could think outside the box.
Coerco has been creating custom-designed products for the mining industry for more than 15 years, handling every aspect of each project in-house, including sourcing materials, design, moulding, fabrication and delivery. This adaptability in manufacturing enabled Coerco to fabricate a new Multi Float® mould that could quickly produce the large number of pipe floats required for the project.
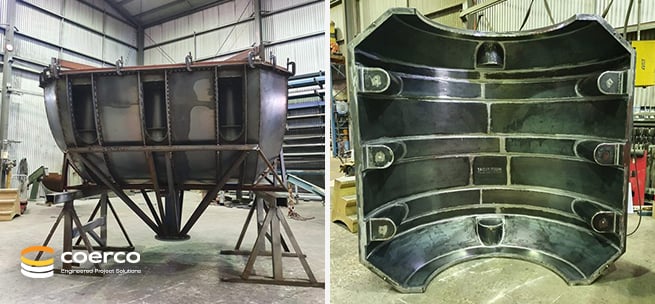
Dozens of giant pipe floats get final checks and testing
The outer skin of the Multi Float® is approximately 17 millimetres thick and made of a tough hexene polyethylene resin, which is the same material used throughout Coerco's large range of liquid management products. Internal test results confirm the material retains 100 percent of its original tensile elongations after 20,000 hours of exposure.
It is manufactured to international standards, UV-stabilised for a performance level of UV20 to protect against degradation and is chemical resistant. Internally, the Multi Float® was injected with a marine-grade polyurethane closed cell foam which ensures buoyancy even if the outer skin is compromised. Two separate pipe diameters were floated with these pipe floats being, 1200 millimetres and 1000 metre diametres.
Included in each Multi Float® is an internal anti-slip mechanism and galvanised fasteners for easy assembly on site.
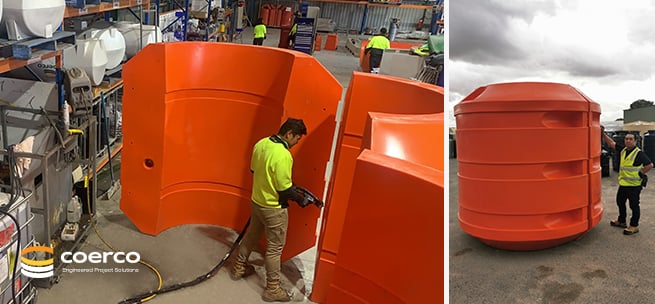
Overseas transport logistics organised in-house
Each assembled Multi Float® weighed up to 515kg and measured more than two metres in height and width. As delivery is a standard part of the service at Coerco, the company filled 14, 40 foot shipping containers with six half sections each, totalling 170 halves.
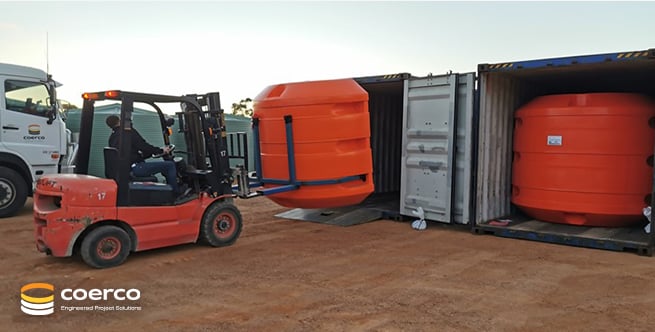
The dewatering system supports processing at the mine, which spans 13,600 hectares and is divided into four zones with its main deposits located at Balboa, Botija, Colina and Valle Grande. Commercial production at the mine started in June 2019 and the plant will produce more than 300,000 tonnes of copper per year from 85 million tonnes of ore processed annually.
.jpg?width=655&height=332&name=Image-3%20(2).jpg)
Along with copper, the mine also produces gold, silver and molybdenum, has a 34-year mine life and has an estimated 3.1 billion tonnes of proven and probable reserves.
Comments